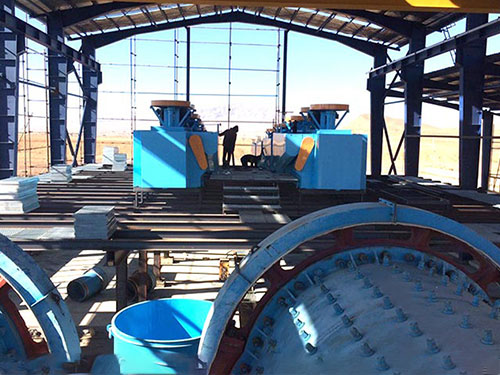
Ceramic Ball Mill Machine: The Ultimate Guide for Efficient Grinding
Introduction to Ceramic Ball Mill Machines
Ceramic ball mill machines are specialized grinding equipment designed for processing delicate, high-purity materials across various industries. Unlike conventional steel ball mills, these machines utilize ceramic linings and grinding media to prevent contamination - making them ideal for ceramics, paints, pharmaceuticals, and food processing. This comprehensive guide explores ceramic ball mill technology, its advantages, applications, and optimization techniques.
How Ceramic Ball Mills Work
Unique Grinding Mechanism
Material Loading: Powder or slurry enters the ceramic-lined chamber
Gentle Grinding: Ceramic balls (alumina/zirconia) provide impact and attrition
Controlled Processing: Adjustable rotation (20-40 RPM) prevents overheating
Pure Discharge: Contamination-free product output
Key Technical Specifications:
Capacity range: 5L to 10,000L
Grinding fineness: 1-50μm achievable
Temperature control: ±2°C precision
Noise level: <65dB (quieter than steel mills)
Critical Components of Ceramic Ball Mills
Component | Material Options | Function |
---|---|---|
Mill Liner | Alumina (92-99%) | Prevents metal contamination |
Grinding Media | Zirconia/Silica | Chemically inert grinding |
Drive System | Variable frequency | Precise speed control |
Sealing System | PTFE/Gasket | Maintains sterile environment |
Cooling Jacket | Stainless steel | Temperature regulation |
Top Applications of Ceramic Ball Mills
1. Advanced Ceramics Manufacturing
Grinding technical ceramics
Preparing ceramic glazes
Producing electronic ceramics
2. Pharmaceutical Industry
Nanoparticle production
Active ingredient milling
Vaccine adjuvant preparation
3. Food & Cosmetic Processing
Chocolate refining
Food color grinding
Cosmetic powder production
4. Specialty Chemicals
Catalyst preparation
Pigment dispersion
Battery material processing
Advantages Over Conventional Ball Mills
✔ Zero Metal Contamination - Essential for high-purity applications
✔ Corrosion Resistance - Handles acidic/alkaline materials
✔ Temperature Control - Prevents thermal degradation
✔ Longer Service Life - 3-5x durability vs steel mills
✔ Customizable Fineness - Adjustable for nano/micro grinding
Optimizing Ceramic Ball Mill Performance
Media Selection Guide
Alumina Balls (92%): Standard for most applications
Zirconia Balls: Higher density for faster grinding
Silicon Nitride: Extreme wear resistance
Yttria-Stabilized: For ultra-fine grinding
Operational Best Practices
Maintain 30-50% media filling ratio
Control slurry density (65-75% solids ideal)
Regular media size distribution checks
Monitor liner wear every 200-300 hours
Maintenance Protocol
Monthly: Inspect ceramic liners for cracks
Quarterly: Replace worn media (>15% weight loss)
Biannually: Check drive alignment
Annually: Full system recalibration
Industry-Specific Configuration Tips
For Electronic Ceramics:
Use 99% alumina liners
Ultra-fine zirconia media
Argon atmosphere option
For Pharmaceutical Use:
CIP/SIP compatible designs
FDA-compliant materials
Isolator integration
Emerging Technological Advancements
🔹 Smart Monitoring Systems - Real-time particle size analysis
🔹 Self-Cleaning Designs - Automated maintenance cycles
🔹 Hybrid Drives - 30% energy savings
🔹 Nano-Coated Liners - Extended 2x service life
Selecting the Right Ceramic Ball Mill
Key Considerations:
Material purity requirements
Batch vs continuous operation
Required production capacity
Temperature sensitivity
Cleanroom compatibility
Future scalability
Ceramic ball mill machines represent the gold standard for contamination-sensitive grinding applications across multiple high-tech industries. Their unique combination of material purity, precise control, and process flexibility makes them indispensable for manufacturers requiring absolute product integrity.
When investing in ceramic ball milling technology, partnering with experienced suppliers ensures optimal machine configuration for specific material characteristics and production goals. Properly selected and maintained ceramic ball mills deliver consistent, high-quality results while minimizing operational costs over their extended service life.
For operations requiring contamination-free grinding solutions, ceramic ball mills offer unmatched performance advantages that directly translate to superior product quality and manufacturing efficiency.