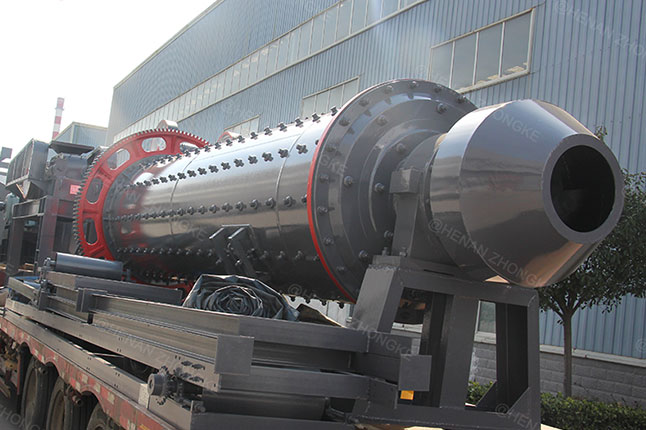
Ball Mill for Wet Grinding: A Comprehensive Guide
Introduction
A ball mill for wet grinding is a crucial equipment in mineral processing, ceramics, and chemical industries. Unlike dry grinding, wet grinding involves the use of liquid (usually water) to facilitate particle size reduction, enhance material flow, and improve milling efficiency.
This guide explores:
How a wet grinding ball mill works
Key advantages over dry grinding
Applications in various industries
How Does a Ball Mill for Wet Grinding Work?
A ball mill for wet grinding operates by rotating a cylinder filled with grinding media (steel or ceramic balls) and the material to be ground, mixed with water or another liquid.
Key Components:
Rotating Drum – Contains the grinding media and raw material slurry.
Grinding Media – Balls (steel, ceramic, or pebbles) that crush and grind the material.
Drive System – Motor and gearbox to rotate the drum.
Discharge Mechanism – Grate or overflow design for slurry output.
Wet Grinding Process Steps:
Material Feeding – The raw material is mixed with liquid (water or solvent) to form a slurry.
Grinding Action – The rotating drum lifts and drops the grinding balls, crushing particles through impact and abrasion.
Slurry Discharge – The finely ground slurry exits through the discharge end for further processing.
Advantages of Wet Grinding Ball Mills
Compared to dry grinding, a ball mill for wet grinding offers several benefits:
✅ Higher Efficiency – Water reduces particle agglomeration, improving grinding effectiveness.
✅ Finer Particle Size – Achieves sub-micron levels, ideal for paints, ceramics, and pharmaceuticals.
✅ Lower Heat Generation – Liquid cooling prevents overheating, protecting sensitive materials.
✅ Reduced Dust Pollution – Minimizes airborne particles, enhancing workplace safety.
✅ Better Material Flow – Slurry handling is easier compared to dry powders.
Applications of Wet Grinding Ball Mills
A ball mill for wet grinding is widely used in:
1. Mining & Mineral Processing
Gold, Copper, Iron Ore: Wet grinding improves liberation of valuable minerals from ore.
Limestone & Cement: Produces fine slurry for better reactivity.
2. Ceramics & Paints
Glazes & Pigments: Ensures ultra-fine particle distribution for smooth finishes.
Inks & Coatings: Provides consistent viscosity and color dispersion.
Choosing the Right Ball Mill for Wet Grinding
When selecting a wet grinding ball mill, consider:
1. Material Hardness & Feed Size
Soft materials (e.g., limestone) → Rubber-lined mills
Hard materials (e.g., quartz) → Steel-lined mills
2. Grinding Media Selection
Steel Balls – High density, ideal for metals and hard minerals.
Ceramic Balls – Non-contaminating, used in food and pharma.
Zirconia Balls – Wear-resistant for ultra-fine grinding.
3. Mill Size & Capacity
Small labs → Bench-top ball mills (1–10 liters)
Industrial use → Large-scale mills (up to 30,000 liters)
4. Discharge Mechanism
Overflow Type – Best for fine grinding.
Grate Discharge – Suitable for coarse materials.
5. Energy Efficiency
Look for variable speed drives and high-efficiency motors to reduce power consumption.
Maintenance Tips for Longevity
To maximize the lifespan of your ball mill for wet grinding:
🔧 Regular Lubrication – Prevent bearing failures.
🔧 Inspect Liners & Media – Replace worn-out balls and liners.
🔧 Monitor Slurry Density – Optimize grinding efficiency.
🔧 Clean Discharge Screen – Avoid clogging.
Conclusion
A ball mill for wet grinding is essential for industries requiring ultra-fine, consistent particle sizes. Its advantages—higher efficiency, finer output, and better material handling—make it superior to dry grinding in many applications.
When choosing a mill, consider material type, capacity, and energy efficiency. Proper maintenance ensures peak performance and longevity.