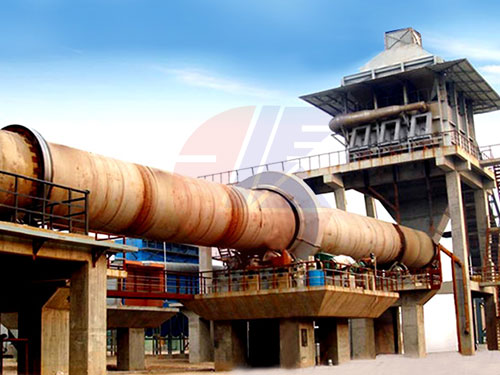
Active Lime Production Line Rotary Kiln: The Complete Guide to Efficient Calcination
Introduction to Active Lime Production Line Rotary Kilns
Active lime production line rotary kilns are the core equipment in modern lime manufacturing, transforming limestone into high-quality quicklime through precise thermal processing. These industrial-scale kilns offer superior efficiency compared to traditional shaft kilns, making them essential for steel, chemical, and environmental industries. This guide explores rotary kiln technology for active lime production, covering working principles, system components, and optimization strategies.
How Rotary Kilns Work in Active Lime Production
The Calcination Process
Preheating Zone (800-1000°C): Limestone is preheated by exhaust gases
Calcining Zone (1000-1200°C): CO₂ is released, creating CaO (quicklime)
Cooling Zone: Quicklime is cooled before discharge
Key Technical Parameters:
Temperature range: 1050-1250°C
Residence time: 2-4 hours
Production capacity: 100-1200 tpd
Fuel consumption: 115-130kg coal/ton lime
Rotary Kiln System Components
Component | Function | Importance |
---|---|---|
Rotary Drum | Primary reaction chamber | 3-6% slope for material flow |
Support Rollers | Bear kiln weight | Critical for stable rotation |
Drive System | Powers rotation | Variable speed control (0.5-2 rpm) |
Burner | Provides heat | Multi-fuel capability (gas/coal/oil) |
Preheater | Recovers waste heat | Improves energy efficiency by 30-40% |
Cooler | Cools product | Recovers heat for combustion air |
Types of Rotary Kilns for Lime Production
1. Parallel Flow Regenerative Kilns
Twin kiln configuration
Heat exchange efficiency >80%
Lowest energy consumption option
2. Preheater Rotary Kilns
2-5 stage cyclone preheaters
30-40% fuel savings
Suitable for medium-large plants
3. Long Rotary Kilns
Traditional design (L/D ratio 30-40)
Simple operation
Lower capital cost
Advantages of Rotary Kilns for Active Lime Production
✔ High Product Quality: 90-95% active lime content
✔ Fuel Efficiency: Advanced systems achieve <120kg coal/ton
✔ Production Flexibility: Handles 20-100mm limestone feed
✔ Environmental Compliance: Lower emissions than shaft kilns
✔ Automation Capability: PLC-controlled operation
Optimizing Rotary Kiln Performance
Key Operational Parameters
Maintain proper temperature profile
Control excess air ratio (1.05-1.15)
Optimize rotation speed
Monitor material retention time
Maintenance Best Practices
Regular refractory lining inspection
Roller alignment checks
Gear lubrication monitoring
Thermal imaging surveys
Energy Saving Techniques
Install waste heat recovery systems
Use high-efficiency burners
Implement advanced process control
Optimize preheater design
Common Production Challenges & Solutions
Issue | Causes | Remedies |
---|---|---|
Ring formation | Overheating | Adjust temperature profile |
Low activity | Insufficient calcination | Increase residence time |
High fuel use | Poor heat recovery | Upgrade preheater system |
Refractory wear | Thermal cycling | Use better quality materials |
Future Trends in Lime Kiln Technology
🔹 AI-Powered Optimization: Machine learning for process control
🔹 Alternative Fuels: Hydrogen and biomass combustion
🔹 Carbon Capture: Integrated CCS systems
🔹 Modular Designs: Prefabricated kiln systems
Selecting the Right Rotary Kiln System
Consider these factors for your active lime production line:
Required production capacity
Limestone characteristics
Available fuel types
Environmental regulations
Automation requirements
Budget constraints
Modern rotary kilns represent the most advanced technology for active lime production, offering superior efficiency, product quality, and environmental performance compared to traditional methods. By understanding the operational principles and maintenance requirements, operators can maximize kiln productivity while minimizing energy consumption and downtime.
For companies planning new lime production facilities or upgrading existing ones, consulting with rotary kiln specialists can help select the optimal system configuration for specific production needs and local conditions. Properly designed and operated rotary kiln systems deliver reliable, cost-effective lime production for decades of service.