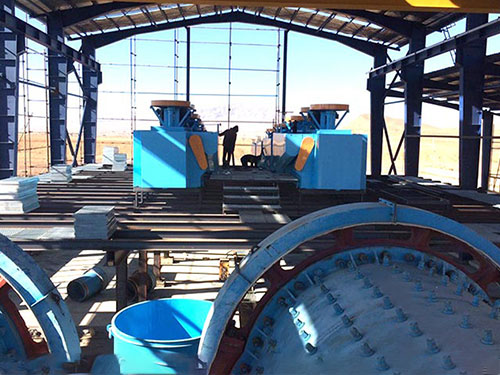
Ore Grinding Ball Mill: The Ultimate Guide for Efficient Mineral Processing
Introduction to Ore Grinding Ball Mills
Ore grinding ball mills are essential equipment in mining and mineral processing operations. These robust machines grind mined ore into fine particles, enabling efficient extraction of valuable metals and minerals. This comprehensive guide explores how ore grinding ball mills work, their key components, benefits, and best practices for optimal performance.
How an Ore Grinding Ball Mill Works
The ore grinding process follows these key steps:
Material Feeding: Raw ore enters the mill through a feed chute
Grinding Action: Steel balls inside the rotating mill crush and grind the ore
Particle Reduction: Continuous impact and attrition break down ore particles
Discharge: Ground material exits through discharge grates
Critical Operating Parameters:
Rotation speed (typically 65-80% of critical speed)
Ball size distribution (25-150mm diameter)
Mill filling percentage (30-45% of mill volume)
Ore feed size and hardness
Key Components of an Ore Grinding Ball Mill
Component | Function | Importance |
---|---|---|
Mill Shell | Structural housing | Withstands grinding forces |
Liners | Protect inner shell | Reduce wear, improve efficiency |
Grinding Media | Steel balls for crushing | Primary grinding mechanism |
Bearings | Support rotation | Critical for smooth operation |
Drive System | Powers rotation | Gears/motors determine speed |
Feed/Discharge | Material flow control | Maintains processing rate |
Types of Ore Grinding Ball Mills
1. Overflow Ball Mills
Continuous operation
Simpler design
Suitable for fine grinding
2. Grate Discharge Ball Mills
Controlled particle discharge
Better for coarse grinding
Higher capacity than overflow mills
3. Peripheral Discharge Mills
Unique discharge mechanism
Handles abrasive ores well
Specialized applications
Benefits of Using Ball Mills for Ore Grinding
✔ High Capacity Processing: Handles large volumes of ore
✔ Precise Particle Control: Achieves desired fineness (typically 10-300μm)
✔ Material Versatility: Processes various ore types (gold, copper, iron, etc.)
✔ Proven Reliability: Simple, robust design with long service life
✔ Scalability: Available in sizes from lab-scale to 8+ meter diameters
Optimizing Ball Mill Performance
Grinding Media Selection
Forged steel balls: Most common, good wear resistance
High-chrome alloy: Better wear life for abrasive ores
Ceramic balls: For contamination-sensitive applications
Optimal Operating Conditions
Maintain proper ball charge (30-32% of mill volume)
Control feed rate to prevent over/under loading
Monitor power draw for efficiency
Regularly measure product fineness
Maintenance Best Practices
Inspect liners every 2-3 months
Monitor bearing temperatures
Lubricate gears regularly
Check bolt tensions
Common Challenges and Solutions
Problem | Cause | Solution |
---|---|---|
Low throughput | Improper feed size | Optimize crusher settings |
High energy use | Incorrect ball charge | Adjust media size/distribution |
Liner wear | Abrasive ore | Use wear-resistant materials |
Vibration | Mechanical issues | Check alignment, bearings |
Future Trends in Ore Grinding Technology
🔹 Advanced Control Systems: AI-powered optimization
🔹 High-Efficiency Designs: Reduced energy consumption
🔹 Wear-Resistant Materials: Longer-lasting components
🔹 Hybrid Grinding: Combining ball mills with other technologies
Selecting the Right Ore Grinding Ball Mill
Consider these factors when choosing equipment:
Ore characteristics (hardness, abrasiveness)
Required production capacity
Desired product fineness
Available space and infrastructure
Energy efficiency requirements
Ore grinding ball mills remain the workhorse of mineral processing plants worldwide. Their ability to efficiently reduce ore particles to liberation sizes makes them indispensable in mining operations. By understanding proper operation, maintenance, and optimization techniques, operators can maximize productivity while minimizing costs.
For operations looking to improve grinding efficiency or upgrade equipment, consulting with ball mill specialists can help identify the best solutions for specific ore processing needs.