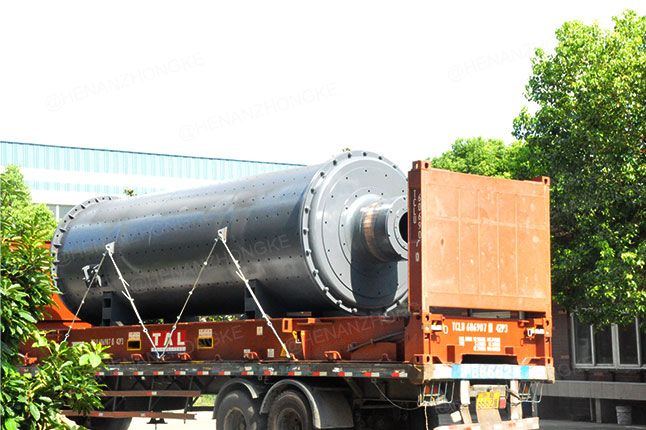
Ball mills are crucial equipment in various industries, including mineral processing, building materials, and chemical production. They play a vital role in grinding materials to the desired particle size. However, their operational efficiency often leaves room for improvement. This article discusses strategies for optimizing ball mill performance to enhance efficiency and reduce costs.
1. Adjust Rotating Speed
One of the key factors affecting ball mill efficiency is the rotating speed. Adjusting the rotating speed can significantly impact the grinding process. A higher rotating speed can increase the collision frequency between the balls and the materials, thereby enhancing grinding efficiency. However, too high a speed may lead to excessive wear and tear on the equipment and increased energy consumption. Therefore, finding the optimal rotating speed is crucial for balancing efficiency and cost1.
2. Optimize Ball and Feed Particle Size Distribution
The size distribution of both the balls and the feed particles plays a significant role in determining the milling efficiency. A well-chosen ball size distribution can ensure more effective grinding, while an appropriate feed particle size can reduce the workload on the ball mill and improve grinding efficiency. Research has shown that an attainable region approach can be used to optimize these parameters, leading to improved milling performance2.
3. Implement Online Ball and Pulp Measurements
Advanced technology, such as online ball and pulp measurements, can provide real-time data on the grinding process. This information can be used to adjust operational parameters in real-time, ensuring optimal performance. By monitoring key indicators like ball load, pulp density, and grinding efficiency, operators can make informed decisions to maximize efficiency and minimize costs3.
4. Reduce Energy Consumption
Ball mills are significant energy consumers. Reducing energy consumption is not only beneficial for the environment but also helps in lowering operational costs. This can be achieved by optimizing the grinding process, using energy-efficient motors, and implementing variable frequency drives (VFDs) to adjust the motor speed according to the load. Additionally, regular maintenance and upgrades to the ball mill can reduce friction and wear, further lowering energy consumption.
5. Improve Feed Point Design
The design of the feed point in a ball mill can significantly affect its performance. An inefficient feed point can lead to uneven material distribution and reduced grinding efficiency. Improving the feed point design can ensure more uniform material feed, leading to better grinding results and increased efficiency. This may involve modifications to the feed chute or the introduction of advanced feeding systems4.
In conclusion, optimizing ball mill performance involves a combination of strategies, including adjusting rotating speed, optimizing ball and feed particle size distribution, implementing online measurements, reducing energy consumption, and improving feed point design. By adopting these practices, industries can enhance the efficiency of their ball mills, reduce costs, and improve overall profitability.