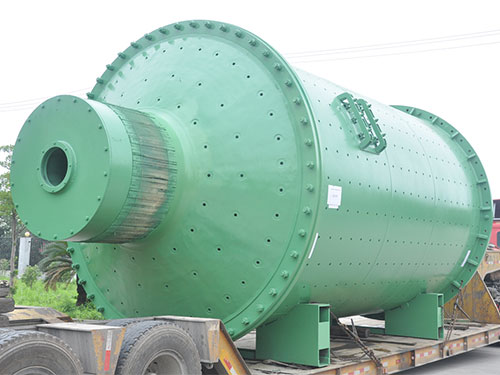
The Ultimate Guide to Ball Mill for Grinding: Principles, Types, and Applications
Introduction
Ball mills are essential equipment in mineral processing, cement production, and chemical industries for grinding materials into fine powders. The ball mill for grinding is widely used due to its efficiency, versatility, and ability to handle both wet and dry processes. This article explores the working principles, types, advantages, and key applications of ball mills in various industries.
How Does a Ball Mill Work?
A ball mill for grinding operates by rotating a cylindrical shell partially filled with grinding media (usually steel or ceramic balls). As the mill rotates, the balls cascade and impact the material, breaking it down into smaller particles through:
Impact – The balls drop from the top of the shell, crushing the material.
Attrition – Friction between particles and grinding media refines the material.
Compression – Larger particles are crushed between the balls and the mill lining.
The efficiency of grinding depends on factors like rotational speed, ball size, material feed rate, and the hardness of the grinding media.
Types of Ball Mills
1. Horizontal Ball Mill
Most common type, used in mining and cement industries.
Suitable for both wet and dry grinding.
Available in batch or continuous operation modes.
2. Vertical Ball Mill
Compact design, often used for fine and ultra-fine grinding.
Lower energy consumption compared to horizontal mills.
Ideal for laboratory and small-scale production.
3. Planetary Ball Mill
High-energy grinding for nanomaterials and mechanical alloying.
Multiple jars rotate on a sun wheel, enhancing grinding efficiency.
Used in pharmaceuticals, ceramics, and advanced materials research.
4. Vibratory Ball Mill
Uses vibration instead of rotation for ultrafine grinding.
Faster and more efficient for certain materials like pigments and chemicals.
Advantages of Using a Ball Mill for Grinding
✔ High Efficiency – Capable of producing fine and ultra-fine powders.
✔ Versatility – Works with wet or dry materials, abrasive or brittle substances.
✔ Scalability – Available in lab-scale to industrial-scale models.
✔ Low Contamination – Ceramic or rubber linings reduce metal contamination.
✔ Adjustable Fineness – Particle size can be controlled by adjusting grinding time and media size.
Key Applications of Ball Mills
1. Mining & Mineral Processing
Grinding ores (gold, copper, iron) for further extraction.
Used in flotation and leaching processes.
2. Cement Industry
Crushing and grinding clinker into cement powder.
Blending raw materials before kiln processing.
3. Chemical & Pharmaceutical Industry
Producing fine chemicals, dyes, and pharmaceutical powders.
Ensuring uniform particle size for better drug dissolution.
4. Ceramics & Paints
Grinding pigments and ceramic materials for smooth finishes.
Used in glaze preparation and advanced ceramic manufacturing.
Choosing the Right Ball Mill
When selecting a ball mill for grinding, consider:
Material Hardness – Determines the type of grinding media (steel, ceramic, or alumina).
Desired Particle Size – Influences mill speed and grinding duration.
Batch vs. Continuous Processing – Depends on production scale.
Wet vs. Dry Grinding – Wet milling reduces dust but requires drying steps.
The ball mill for grinding remains a cornerstone in material processing across multiple industries. Its ability to produce fine and uniform particles efficiently makes it indispensable in mining, cement, pharmaceuticals, and ceramics. By understanding the different types and their applications, businesses can optimize their grinding processes for better productivity and cost-effectiveness.
For high-performance ball mills, always choose reputable manufacturers that offer durable construction, energy-efficient designs, and customizable options to meet specific grinding needs.